In today’s cost-conscious aviation maintenance landscape, Airplane Engine Stands for Lease offer a smart solution for small workshops looking to maximize efficiency while minimizing capital expenditure. The specialized equipment required for safe engine handling represents a significant investment that many smaller operations struggle to justify, especially for stands that may only see occasional use. Savvy maintenance managers are discovering the budget advantages of jet engine stands for lease rather than committing to outright purchases.
When maintaining aircraft engines, having access to the right equipment like those offered at https://stands.aero/product/pw1100/ ensures both safety and efficiency without tying up valuable capital. This approach has become increasingly popular as maintenance facilities focus on their core competencies and seek to optimize their financial resources.
The Financial Case for Leasing Engine Stands
Direct ownership of engine stands comes with substantial hidden costs that extend far beyond the initial purchase price. These ongoing expenses can significantly impact the bottom line of small aviation workshops that operate with tight margins.
Understanding the True Cost of Ownership
When calculating the real cost of owning engine stands, maintenance managers must consider several factors that affect long-term financial planning:
- Initial capital investment (often $30,000-$100,000+ per specialized stand)
- Regular maintenance and certification costs
- Storage space requirements and associated facility expenses
- Insurance and depreciation
- Opportunity cost of capital that could be invested elsewhere
The financial burden becomes even more apparent for specialized stands that may only be used a few times yearly. Leasing eliminates these concerns by converting a major capital expense into a predictable operational cost that scales with actual usage.
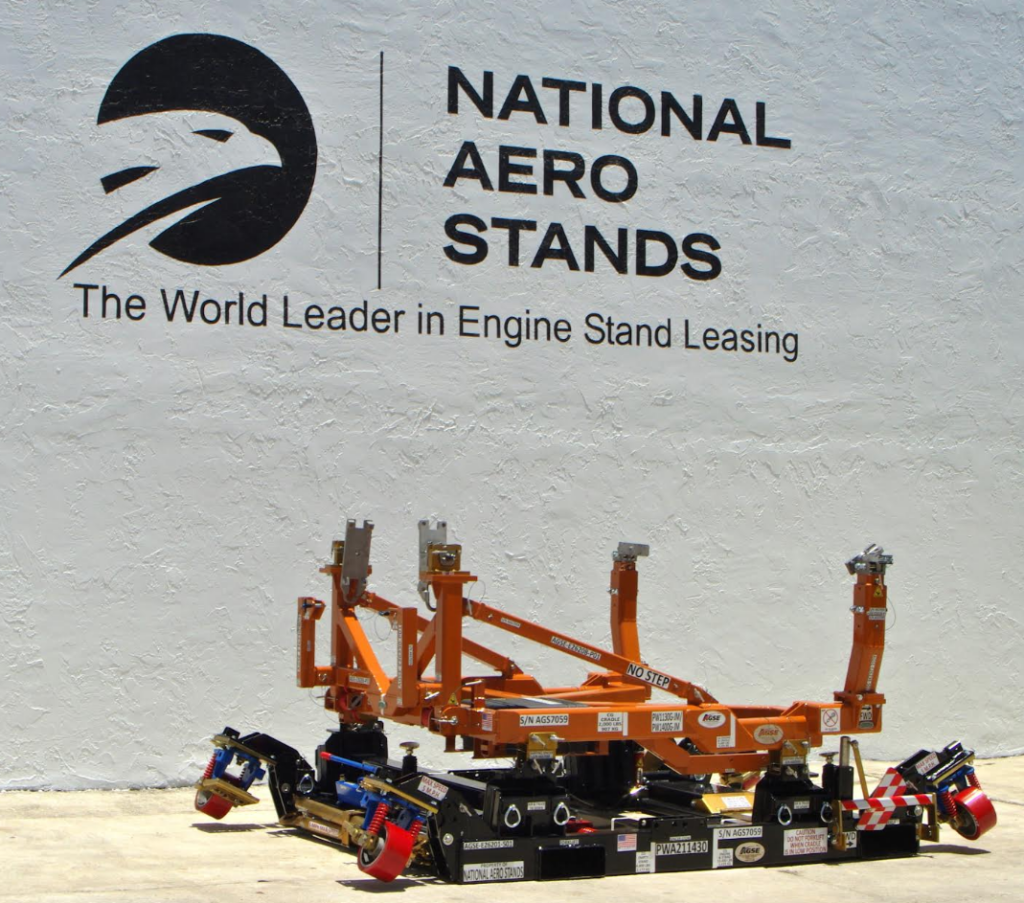
Strategic Planning for Cost Optimization
Smart planning can dramatically reduce the costs associated with engine stand leasing. Taking a proactive approach to maintenance scheduling allows small workshops to maximize efficiency and minimize expenses through several proven strategies.
Maximizing Lease Efficiency
Before arranging for engine stand leasing, consider implementing these cost-saving approaches that help streamline the process:
- Book stands well in advance when possible to secure better rates
- Consolidate maintenance schedules to reduce the number of lease periods
- Negotiate flexible terms for extensions if maintenance timelines shift
- Consider multi-stand packages when several engines require service
- Develop relationships with providers for potential loyalty discounts
Ownership vs. Leasing: Cost Comparison
When evaluating whether to purchase or lease engine stands, small aviation workshops must analyze both direct and indirect costs. The following table provides a comprehensive comparison of the financial implications of each approach:
Cost Factor | Ownership | Leasing |
---|---|---|
Initial Capital Outlay | $30,000-$100,000+ | $0 (reservation deposit only) |
Annual Storage Costs | $2,500-$5,000 | $0 |
Maintenance & Certification | $1,000-$3,000 annually | Included in lease price |
Insurance | $500-$1,500 annually | Typically covered by lessor |
Transportation Between Facilities | Full responsibility of owner | Often arranged by leasing company |
Depreciation | 5-10% annually | Not applicable |
Utilization Efficiency | Often < 30% for small shops | 100% during lease period |
This comparison clearly demonstrates why leasing has become the preferred option for operations that don’t maintain a constant high-volume engine maintenance schedule13.
Practical Implementation for Small Workshops
Small aviation maintenance operations face unique challenges when it comes to equipment management. Working with limited space and capital requires creative solutions that maximize efficiency without compromising quality or safety.
Optimizing Workshop Operations
The decision to lease rather than purchase engine stands affects multiple aspects of workshop management. Consider these practical adjustments to your operations:
- Repurpose storage space previously used for stands for revenue-generating activities
- Develop standardized procedures for requesting, receiving, and returning leased equipment
- Train staff on efficient engine handling to minimize lease duration
- Create partnerships with nearby facilities to potentially share shipping costs
- Implement tracking systems to analyze usage patterns and optimize future leasing decisions
Shipping costs represent a significant portion of the total expense when leasing engine stands. Due to their size and specialized nature, these stands require careful logistics planning to avoid unnecessary expenses.
Transportation Cost Management
Understanding the logistics aspects of engine stand leasing can help small workshops significantly reduce their overall expenses. Before finalizing any lease agreement, explore these cost-saving logistics strategies:
- Compare shipping quotes from multiple providers rather than accepting the lessor’s default option
- Consider ground transportation for regional movements instead of air freight
- Plan return shipping well in advance to avoid rush fees
- Investigate backhaul opportunities with regular freight partners
- Explore the possibility of picking up and returning stands yourself for local providers
Frequently Asked Questions
What is the typical lease duration for an engine stand?
Most providers offer flexible lease terms starting from 30 days, with common increments of 30, 60, or 90 days. Some companies now offer custom durations to better accommodate specific maintenance schedules and reduce costs for shorter projects.
Are there emergency options for AOG situations?
Yes, most reputable engine stand leasing companies offer expedited services for Aircraft On Ground situations. These services typically guarantee delivery within 24 hours but come with premium pricing due to the urgent nature of the request.
Who handles maintenance and certification of leased stands?
The lessor typically manages all maintenance, certification, and insurance requirements. This represents a significant advantage of leasing, as it eliminates these administrative and financial burdens from the workshop’s responsibilities.
Can leasing companies help with customs clearance for international shipping?
Most established leasing providers offer comprehensive support for international transactions, including documentation assistance and customs clearance guidance. This expertise can prevent costly delays when working across borders.
Embracing the Leasing Advantage
For small aviation workshops, the decision to lease engine stands rather than purchase them outright represents a strategic approach to resource management. By converting a major capital expense into a flexible operational cost, these businesses can improve cash flow, reduce financial risk, and focus their resources on core competencies.
The aviation maintenance industry continues to evolve toward specialized services and efficient resource allocation. By embracing the leasing model for specialized equipment like engine stands, small workshops position themselves to remain competitive while delivering high-quality service without the burden of unnecessary overhead costs.